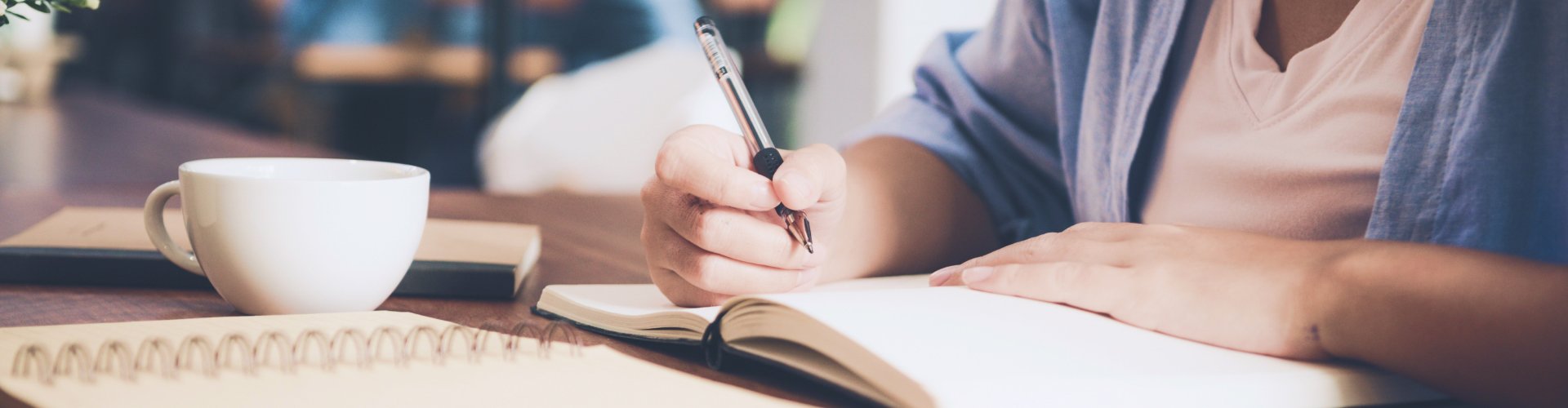
Semi-welded Plate Heat Exchanger: The Outstanding Choice in the Industrial Heat Exchange Field
Ⅰ. The Unique Structure of the Semi-welded Plate Heat Exchanger
The semi-welded plate heat exchanger combines the advantages of traditional plate heat exchangers and welding technology. It consists of a series of corrugated heat transfer plates. These plates are fixed by a special welding process in some areas, forming a unique structure.
Unlike fully welded heat exchangers, the semi-welded heat exchanger retains the connection of some detachable plates, which gives the device obvious advantages in terms of maintenance and cleaning. At the same time, the corrugated plate design greatly increases the heat transfer area and improves the heat exchange efficiency. The corrugation shape and angle of each plate are carefully designed to promote the formation of turbulent flow of the fluid between the plates, strengthening the heat transfer effect and enabling heat to be transferred quickly and efficiently between different fluids.
Ⅱ. Excellent Performance and Distinct Advantages
1. High-efficiency Heat Transfer
The semi-welded plate heat exchanger has extremely high heat transfer efficiency and can achieve a large amount of heat transfer in a relatively small space. This benefits from its compact structure and efficient heat transfer plate design. Compared with traditional shell-and-tube heat exchangers, the semi-welded plate heat exchanger can complete the same heat exchange task in a shorter time, greatly improving production efficiency. For example, in chemical production, for some reaction processes with strict temperature control requirements, the semi-welded plate heat exchanger can quickly and accurately adjust the temperature of the materials to ensure the smooth progress of the reaction.
2. Strong Flexibility
Due to the detachable nature of some plates, the semi-welded plate heat exchanger shows extremely high flexibility in the face of different production requirements. Users can easily adjust the number and arrangement of plates according to the actual heat exchange needs, thereby changing the heat exchange capacity of the device. This flexibility enables it to adapt to a variety of different process flows and operating conditions. Whether it is large-scale industrial production or small-scale experimental research, a suitable configuration solution can be found.
3. Excellent Corrosion Resistance
In many industrial applications, the fluid is often corrosive, which poses high requirements for the materials and structure of the heat exchanger. Semi-welded plate heat exchangers are usually made of corrosion-resistant materials such as stainless steel and titanium alloy. Moreover, the application of the welding process has greatly improved the sealing performance of the device, effectively preventing the leakage of corrosive fluids and extending the service life of the equipment. In the food and beverage industry, hygienic semi-welded plate heat exchangers can ensure that the parts in contact with food meet strict hygienic standards, and at the same time resist the erosion of corrosive substances such as acids and alkalis that may occur during the food processing process.
4. Energy-saving and Environmentally Friendly
In today's increasingly energy-scarce world, energy conservation and environmental protection have become important themes of industrial development. Thanks to its high heat transfer performance, the semi-welded plate heat exchanger can reduce energy consumption while achieving the same heat exchange effect. At the same time, the compact structural design makes the equipment occupy less space, reducing the costs of plant construction and equipment installation. Moreover, due to its good maintainability and long service life, it reduces the generation of equipment replacement and waste, which is in line with the requirements of sustainable development.
Ⅲ. Wide Range of Application Fields
The excellent performance of the semi-welded plate heat exchanger has made it widely used in many industries.
In the chemical industry, it is used for heat exchange and temperature control in various chemical reaction processes, such as the heating and cooling of distillation towers and the temperature regulation of reactors. In the pharmaceutical industry, it is used for the concentration, cooling, and heating of liquid medicine during the drug production process to ensure the stability and consistency of drug quality. In the food and beverage industry, from the sterilization of milk, the concentration of fruit juice to the brewing of beer, the semi-welded plate heat exchanger plays an important role. In addition, in the field of heating, ventilation, and air conditioning, it is also used in building heating, cooling, and hot water supply systems to provide people with a comfortable indoor environment.
Ⅳ. Key Points of Maintenance and Upkeep
To ensure that the semi-welded plate heat exchanger always maintains good operating conditions, proper maintenance and upkeep are crucial.
Regularly check the sealing performance of the equipment to prevent fluid leakage. For detachable plates, clean them regularly to remove dirt and deposits on the plate surface to maintain good heat transfer performance. At the same time, pay attention to checking whether there is any deformation, damage, etc. of the plates. If there are problems, replace them in a timely manner. During the operation of the equipment, strictly control the temperature, pressure, and flow rate of the fluid to avoid exceeding the design range of the equipment and causing damage to the device.
With its unique structure, excellent performance, and wide range of application fields, the semi-welded plate heat exchanger has become an important device in the modern industrial heat exchange field. It not only provides strong support for enterprises to improve production efficiency and reduce costs but also plays an active role in energy conservation and environmental protection. With the continuous progress of science and technology, it is believed that the semi-welded plate heat exchanger will continue to innovate and improve in the future industrial development, bringing more efficient and reliable heat exchange solutions to more industries.