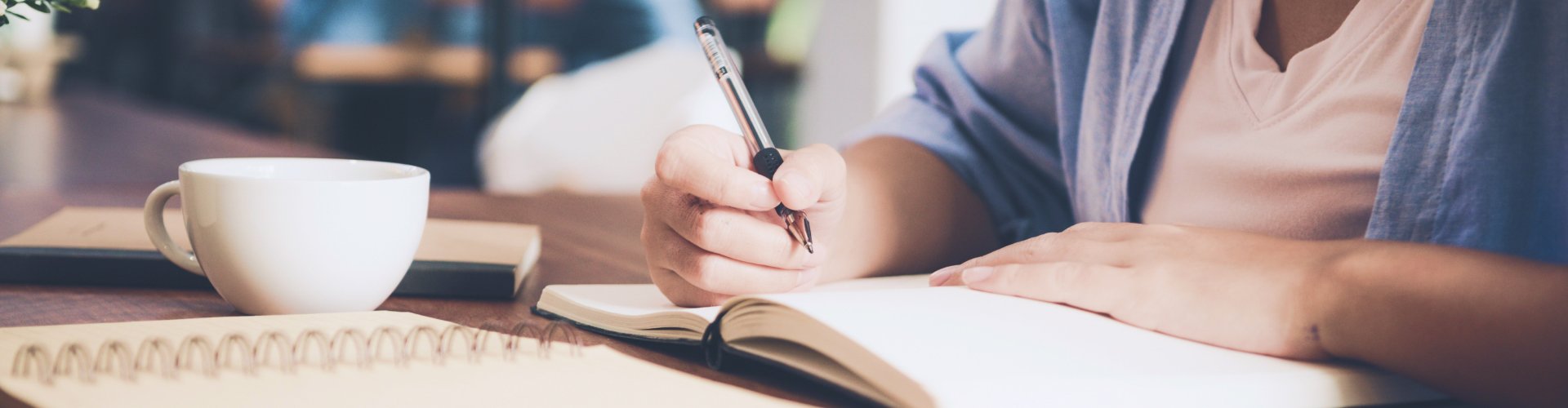
Explore the Brazed Plate Heat Exchanger: Small in Size, but Mighty in Power
Ⅰ. Ingenious Structure: The Wonderful Combination of Metal Sheets
The core of the brazed plate heat exchanger lies in its unique plate structure. One by one, carefully pressed metal sheets, usually made of stainless steel or titanium, are connected like precise jigsaw puzzles to build a "magic space" for heat exchange. The surfaces of the plates are not smooth but are given special textures, either in herringbone or zigzag patterns. Such a design is no accident. When fluids flow through the channels between the plates, these textures act like invisible batons, guiding the fluids to form complex yet orderly turbulent flows. Just like a stream flowing through a well-arranged riverbed, the continuous disturbance and mixing of the fluid greatly enhance the effect of heat transfer. The connection between the plates relies on the brazed welding process. Under the "baptism" of high temperature, the brazing materials tightly weld the plates together, forming an airtight whole. This connection method not only ensures excellent sealing and eliminates the risk of fluid leakage but also enables the heat exchanger to withstand certain pressures and temperatures.
Ⅱ. Wonderful Principle: An Efficient "Heat Transporter"
Its working principle is like an efficient relay race of heat. The hot and cold fluids flow quietly in the adjacent plate channels respectively. Thanks to the extremely thin plates, heat can pass through them at a very high speed from the hot fluid to the cold one. Take the brazed plate evaporator in a refrigeration system as an example. The liquid refrigerant flows slowly in one channel, while the cooled medium, such as air or water, moves simultaneously in the other channel. The refrigerant gradually evaporates under low pressure, greedily absorbing the latent heat of vaporization. And this heat is "ingeniously obtained" from the cooled medium through the thin plates, thus quietly lowering the temperature of the cooled medium. It is precisely the special structure of the plates that causes the fluid turbulence, which is like installing an accelerator for this heat relay race. According to Fourier's law, the significant temperature gradient greatly increases the heat flux density, and naturally, the speed of heat transfer is also greatly enhanced.
Ⅲ. Outstanding Advantages: A Capable Assistant in Multiple Fields
1. High-Efficiency Heat Transfer, an Energy-Saving Pioneer
The combination of its compact plate structure and optimized fluid channel design has enabled its heat transfer coefficient to achieve a qualitative leap compared to the traditional shell-and-tube heat exchanger. Generally speaking, the heat transfer coefficient of the brazed plate heat exchanger can reach 2000 - 5000 W/(m²·K), while that of the shell-and-tube heat exchanger usually only ranges from 10 to 1000 W/(m²·K). This means that for the same heat exchange task, the brazed plate heat exchanger can easily handle it with a smaller heat exchange area, greatly reducing the space occupied by the equipment and the energy consumption, making it a well-deserved energy-saving pioneer.
2. Compact and Space-Saving
Thanks to the thinness and close arrangement of the plates, the brazed plate heat exchanger shows unparalleled advantages in terms of volume and floor space. Its volume is only about 1/5 - 1/3 of that of the shell-and-tube heat exchanger with the same heat exchange capacity. It's like a graceful dancer, moving freely on the stage with limited space. Whether it's in the narrow cabins of ships, the compact spaces of mobile refrigeration equipment, or the limited sites of small industrial installations, it can perform with ease.
3. Corrosion Resistance and Hygienic Excellence
The plates made of high-quality materials such as stainless steel and titanium endow the heat exchanger with excellent corrosion resistance, enabling it to withstand the "attacks" of various corrosive fluids. In industries with strict hygienic requirements such as food and pharmaceuticals, it stands out with its gasket-free design, reducing the breeding ground for bacteria. The smooth surfaces of the plates also make cleaning a breeze, perfectly meeting the high hygienic standards of the industries and being a model of hygiene.
Ⅳ、Wide Applications: A Shining Star in Various Industries
1. Refrigeration and Air Conditioning, Ensuring Comfort
In the vast world of refrigeration systems, the brazed plate heat exchanger plays a pivotal role. Whether it's small split air conditioners or large commercial refrigeration equipment like supermarket freezers and cold storages, it is as crucial as the heart. Through efficient heat exchange, it accurately delivers coolness and comfort to every corner, providing reliable temperature guarantees for people's lives and commercial activities.
2. Chemical and Petrochemical Industries, Optimizing Processes
In the complex production processes of the chemical and petrochemical industries, it is an indispensable master of heat distribution. From the temperature control of chemical reactors to the heat exchange in the fractionation and refining processes of petrochemical products, it performs precisely and efficiently, helping to optimize and upgrade the entire production process and improve product quality and production efficiency.
3. Food and Beverage Industries, Guarding Quality
In the production world of food and beverages, it is a loyal guardian of quality. During the pasteurization process of milk, it can quickly and evenly heat the milk to the appropriate sterilization temperature and then cool it rapidly, maximizing the preservation of the milk's nutrition and flavor. On the production lines of fruit juices, beers and other beverages, it also uses its excellent heat exchange ability to ensure that each product meets strict quality standards.
The brazed plate heat exchanger occupies an important position in the field of industrial heat exchange with its unique charm and outstanding performance. Although it has some limitations, with the continuous development and innovation of technology, I believe it will surely shine even more brightly on the future stage and contribute a continuous stream of "heat" power to the development of more industries.