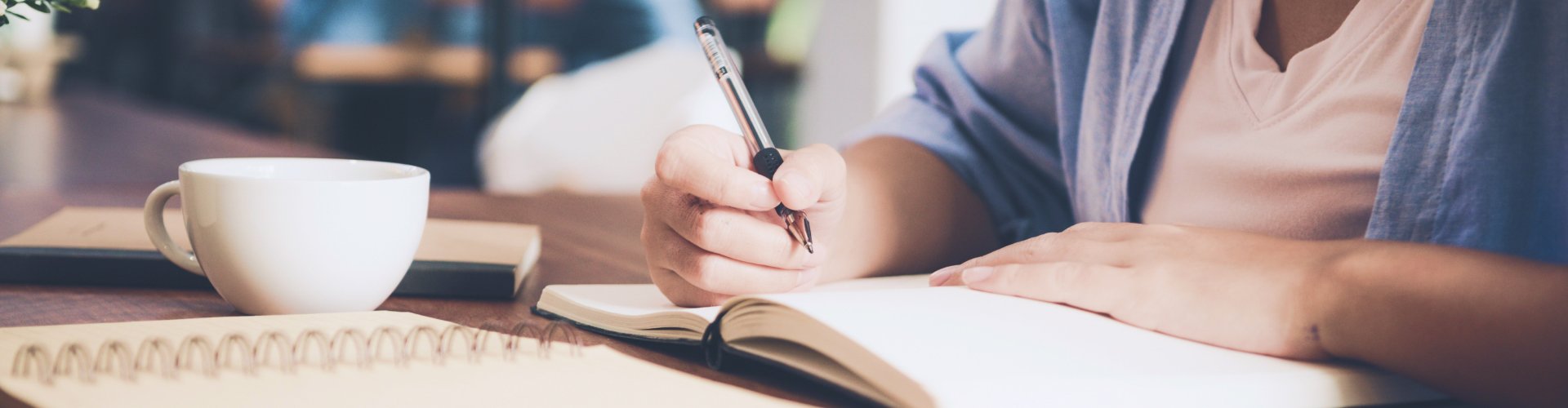
Exploring the Heat Exchanger Plates: The Core Code of Heat Exchange
I. Ingenious Structure, Embedding the Wisdom of Heat Exchange
Heat exchanger plates are usually in the form of thin sheets, made of materials with excellent thermal conductivity and corrosion resistance such as stainless steel and titanium alloy. The surface may seem smooth at first glance, but in fact, it is meticulously designed with unique corrugations or concave-convex patterns. These textures are not for decoration. They greatly increase the heat exchange area of the plates. Imagine crumpling a flat piece of paper. The originally two-dimensional paper surface instantly becomes three-dimensional, and the contact space with the outside world increases significantly. The plates are the same. A larger surface area means that there is a broader "battlefield" for heat transfer, allowing heat to quickly conduct from the hot fluid to the cold fluid, or vice versa.
There are also just the right gaps reserved between adjacent plates to form fluid channels. These channels have an appropriate width, which can not only ensure that the fluid passes through stably at a certain flow rate, forming turbulence and preventing the "dead zones" of heat exchange caused by laminar flow, so that the hot and cold fluids can fully mix and contact; but also will not impose too heavy a burden on the conveying equipment such as pumps due to excessive resistance, perfectly balancing the heat exchange efficiency and operating energy consumption.
II. Diverse Types, Adapted to Different Working Conditions
According to the shape of the corrugations, there are herringbone corrugated plates. Their symmetrical diagonal structures make the fluid flow in a zigzag shape between the plates, and the heat transfer coefficient is high. They are often used in the chemical and pharmaceutical fine chemical industries where high requirements are placed on heat exchange efficiency. For example, in the heat recovery link of precise temperature control during drug synthesis, the herringbone plates help the accurate transfer of heat and reduce energy consumption costs.
There are also horizontal flat corrugated plates. The fluid flow is relatively stable, and the pressure drop is small, which plays a significant role in the HVAC system. In the heat exchange unit of the central air conditioning in office buildings, it ensures the smooth heat exchange between cold water and hot water, creating a comfortable temperature like spring all year round indoors. At the same time, it takes into account energy conservation and reduces the energy consumption of the fan.
From the perspective of the differences in the sealing structure, the gasketed plates rely on elastic gaskets such as rubber to seal the gaps between the plates. The cost is relatively low and the maintenance is convenient. They are suitable for general industrial cooling and domestic hot water preheating scenarios. The circulating water cooling heat exchangers in small and medium-sized factories mostly use this type. In daily maintenance, only the aging gaskets need to be replaced to easily restore the good sealing performance. However, for brazed plates, the plates are permanently connected directly through brazing, without the risk of gasket leakage. They can withstand high temperatures and pressures and play a unique role in the heat exchange link between high-temperature hot oil and low-temperature refrigerant in the petroleum refining industry, ensuring long-term stable operation under complex and harsh process conditions.
III. Daily Maintenance, Continuing the "Vitality" of Heat Exchange
To ensure the continuous and efficient operation of the heat exchanger plates, regular inspections are essential. Regularly check the appearance of the plates for any corrosion spots or cracks. Once the metal luster dims and corrosion pits appear, it is necessary to evaluate the degree of corrosion in a timely manner. For mild cases, chemical cleaning and rust removal can be carried out, and for severe cases, consider replacing the plates to prevent problems such as perforation and leakage, which may lead to a series of problems such as the mixing and pollution of hot and cold fluids and the failure of heat exchange.
For gasketed plates, focus on the aging and deformation of the gaskets. If it is found that the gaskets are hardened and lose their elasticity or have signs of tearing, the machine should be stopped immediately for replacement. When installing, ensure that the gaskets are flat and fit the sealing groove of the plate, and apply an appropriate amount of sealant to enhance the sealing effect, avoiding bypass leakage during operation, which would cause the fluid that should be heat exchanged to "take a shortcut" and reduce the heat exchange efficiency.
The cleaning process is also crucial. Regular chemical cleaning or mechanical cleaning should be carried out according to the working conditions. Chemical cleaning uses acid and alkali cleaning agents to dissolve the dirt and scale on the surface of the plates. However, the concentration, temperature, and cleaning time should be precisely controlled to prevent excessive corrosion. Mechanical cleaning, such as high-pressure water flushing and soft brush wiping, can effectively remove sediment, fiber impurities, and unclog the fluid channels, allowing the plates to "breathe" smoothly and restore their heat exchange vitality.
Although the heat exchanger plates are small, they bear the important task of optimizing energy utilization, promoting industrial progress, and ensuring a comfortable life. Understanding their structure, selection, and maintenance points is just like holding the key to opening the door of efficient heat exchange, helping various industries to save energy and increase efficiency and enjoy the dividends of green development. In the future, with the breakthroughs in material science and manufacturing technology, heat exchanger plates will surely continue to be upgraded and unlock more heat exchange potential. Are you ready to keep up with its innovation pace?