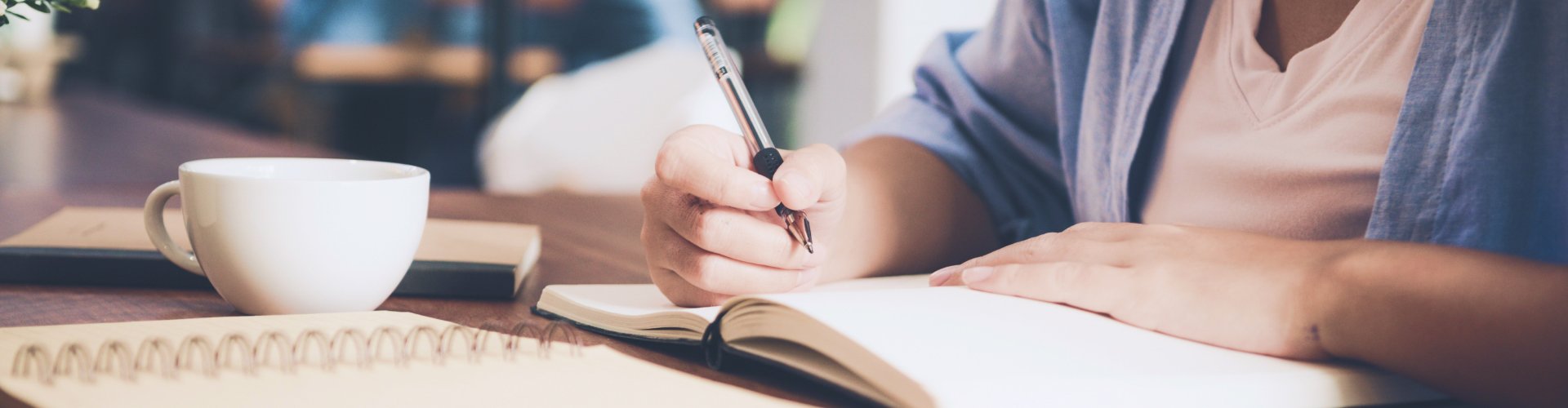
Hiwell Plate heat exchangers have many characteristics:
Superior heat transfer performance
High heat transfer coefficient: The plates of plate heat exchangers are corrugated, causing the fluid to flow in a rotating three-dimensional pattern within the inter-plate channels. This generates turbulence at relatively low Reynolds numbers, enhances fluid agitation, reduces thermal resistance. Generally, the heat transfer coefficient ranges from 1,300 to 4,000 kcal/m²·°C·h, and can reach up to 5,000 kcal/m²·°C·h. Under the same pressure loss, the heat transfer of plate heat exchangers is 6 to 7 times that of shell and tube heat exchangers.
Large logarithmic mean temperature difference, small terminal temperature difference: Plate heat exchangers mostly adopt parallel or countercurrent flow patterns, and their logarithmic mean temperature difference correction factor is usually around 0.95. Moreover, the cold and hot fluids flow parallel to the heat exchange surface without by-pass in plate heat exchangers, resulting in a small terminal temperature difference. For water heat exchange, it can be less than 1°C, while that of shell and tube heat exchangers is generally 5°C.
Low heat loss: Only the periphery of the plates and gaskets are exposed to the air, and the heat loss coefficient is generally only 0.1%, eliminating the need for insulation.
Compact structural design
Small footprint: The plate spacing is generally only 2 - 8 mm, and the corrugations on the plate surface greatly increase the effective heat exchange area, reaching 250 square meters of heat exchange area per cubic meter. To achieve the same heat exchange capacity, the footprint of plate heat exchangers is only 1/3 or even less than that of shell and tube heat exchangers.
Light weight: The thickness of the plates is only 0.4 - 0.8 mm, while the heat exchange tubes of shell and tube heat exchangers have a thickness of 2.0 - 2.5 mm. Moreover, the shell of shell and tube heat exchangers is much heavier than the frame of plate heat exchangers. Generally, plate heat exchangers weigh only about 1/5 of shell and tube heat exchangers.
Convenient operation and maintenance
Great operational flexibility: The heat transfer area can be quickly and effectively increased or decreased by adding or removing plates. The plates can also be rearranged to form new process combinations to adapt to changes in product processes. Intermediate partitions can be set at different positions, enabling a single device to adapt to several media and operations simultaneously, while multiple shell and tube heat exchangers would be required.
Easy installation, inspection and cleaning: There is no need for foundation bolts for installation, and it is easy to disassemble, install, inspect and clean the plates. Due to the smooth plate surface and high degree of turbulence, scaling is less likely to occur. Even if scaling occurs, it is relatively easy to disassemble and clean.
Material and cost advantages
Low metal consumption: For herringbone corrugated plates, excluding the weight of the frame, the metal consumption per square meter of heat exchange is 7.7 kilograms, with a minimum of 7 kilograms per square meter. In contrast, shell and tube heat exchangers of the same parameters have a higher metal consumption.
Low price: Using the same materials and having the same heat exchange area, the price of plate heat exchangers is approximately 40% - 60% lower than that of shell and tube heat exchangers.
Wide range of applications
Diverse media handling: It can handle a variety of media, from water to high-viscosity liquids, even non-Newtonian liquids, and from small-diameter solid particles to suspensions containing fibers.
Rich process applications: It can be used in many continuous reaction processes such as heating, cooling, condensation and evaporation. It is widely used in industrial sectors such as chemical, petroleum, metallurgy, machinery, electric power, food, medicine, shipbuilding, as well as in fields such as HVAC and refrigeration.